纸质工单困住华南汽配龙头,车间数字化破局“交付迷雾”
在华南某知名汽车零部件供应商的生产基地,供应链总监李明刚挂断一个火急火燎的电话:“王总,您要的这批座椅骨架总成的状态,我……我下午一定给您回复!”放下电话,他冲向冲压车间办公室。眼前景象让他心焦:桌上堆满了纸质流转卡、工序单和领料单,几位计划员正满头大汗地在多个Excel表格间切换、拼凑数据。而车间主管老赵正对着厚厚一摞生产指令单发愁:“焊接线需要的冷轧钢卷库存到底够不够?仓库说今天的盘点还没开始!”——这就是“骏驰汽配”的日常写照。尽管公司部署了专业的CRM系统管理主机厂订单、成熟的ERP(如SAP或金蝶)处理财务和供应链,但生产车间的信息“最后一公里”被纸质工单死死卡住,数据链条在此断裂。

一、痛点深渊:被“纸海”吞噬的敏捷与交付
订单进度“两眼一抹黑”:
- 主机厂或一级供应商催问订单状态时,业务员需要电话询问计划部 → 计划员跑去车间抄写工序单上的完成数 → 再找仓库核对半成品库存 → 最后还要确认质检状态。全流程下来,平均耗时超过36小时,严重影响客户信任。
- 主机厂临时追加500套门板订单时,车间因无法实时获取仓库中特定规格镀锌板的准确余量,只能保守拒绝或延迟承诺,错失宝贵的增量机会。
车间、仓库、计划的“信息时差”与“信任危机”:
- 纸质单据流转导致生产、库存数据滞后12小时以上是常态:
- 物料配送员凭经验和“喊话”领料,多次造成关键生产线(如总装线)因缺料停线,损失巨大。
- 成品/半成品入库依赖仓管员手工登记ERP,销售和计划部门经常发现系统库存“虚高”或“找不到实物”,导致发货延误或被主机厂罚款。
- 月底成本核算一团糟:工序单、报废单、返工单未及时上交财务,成本分摊严重失真,难以支撑精准报价。
系统孤岛:CRM/ERP的“失效对接”与计划失效:
- 主机厂订单从CRM系统导入ERP后,仍需人工二次分解、排产,订单转化效率比标杆企业低35%。
- ERP的生产计划模块因缺乏实时车间数据(在制品WIP、设备状态、实际工时),排产准确率不足65%。面对频繁的插单需求(主机厂常态),只能靠经验估算或停工盘点,效率低下,交付风险陡增。
- 车间主任的无奈:“我们就像在给主机厂蒙眼开车——CRM是导航目的地,ERP是规划好的路线图,但车子(车间)的油量(物料)、速度(产能)、路况(异常)全靠猜!”
二、破局关键:三阶打通“智造数据链”
第一步:车间执行数字化——让设备与工人“开口说话”
- 移动端智能报工: 工人通过车间PAD或自带手机(BYOD)扫描工单/产品条码/VIN码关联码,实时反馈工序开始/结束、数量、工时、质检结果(首检、抽检、终检)。
- 设备数据自动采集: 在关键设备(冲压机、焊接机器人、注塑机)加装IoT传感器,自动采集生产数量、设备状态(运行、停机、故障)、稼动率、工艺参数(如焊接电流、温度)。
- 电子工单看板替代纸质: 车间部署大型电子看板,实时显示各产线、工位的生产计划、进度、异常(缺料、设备故障、质量报警)、目标达成率。纸质单据流转成为历史。
- 实施成效(初步): 订单进度查询从“按天计”缩短至“分钟级”,客户催单响应效率提升85%。
第二步:系统融合——拆解“信息烟囱”,构建“数据中枢”
- 核心系统深度集成:
- 主机厂订单/预测从CRM → 自动触发ERP生成生产计划与物料需求计划(MRP)。
- 实时车间报工数据(完成数、工时、状态)→ 自动回写ERP,更新在制品(WIP)库存、消耗物料、计算实际成本。
- 设备状态、质量数据 → 同步至MES(制造执行系统)或数据平台,驱动预警与决策。
- 统一数据平台(数据湖/数据仓库): 汇聚来自CRM、ERP、MES、IoT、物流系统的订单、BOM、工艺、报工、质量、设备、库存、物流信息。
- 360°可视化战情室: 为管理层提供涵盖销售、计划、生产、质量、库存、交付的全维度实时可视化看板,可逐层钻取(Drill Down)至具体工单、设备或产品批次。
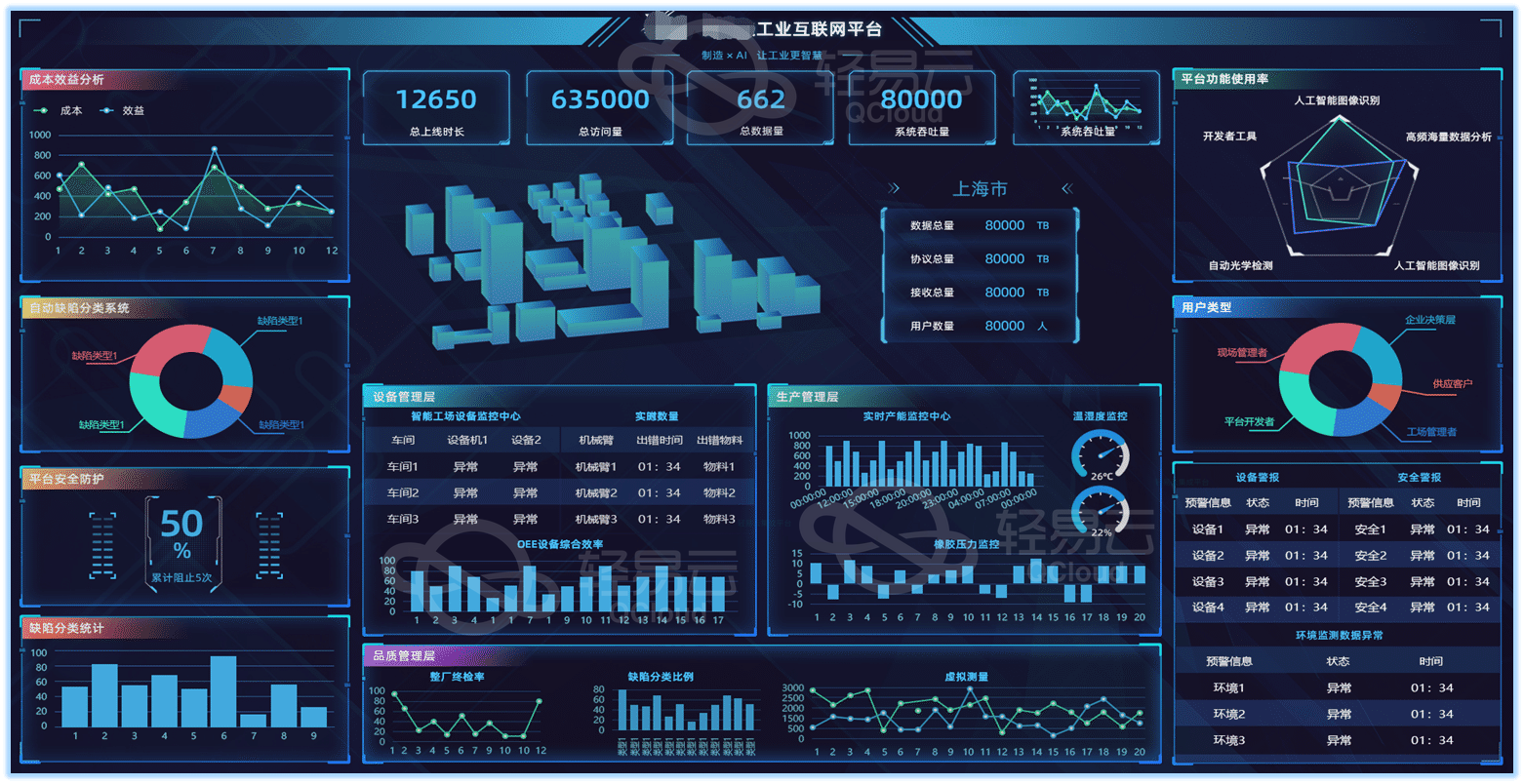
第三步:智能预警——从“被动救火”到“主动防火”
- 动态物料预警: 基于实时生产计划和物料清单(BOM),结合供应商送货信息,系统自动计算物料缺口,提前3天预警采购和计划部门,规避停线风险。
- 交期履约风险雷达: 实时监控订单进度(计划vs实际)、关键路径瓶颈、质量异常频率,自动计算达成概率,触发黄/橙/红三级预警,通知相关负责人提前干预。
- 设备预测性维护: 基于IoT采集的设备运行参数和故障历史,分析潜在故障模式,提前安排维护,减少非计划停机。
三、重生之效:从“交付泥潭”到“敏捷智造”
- 生产透明与效率:
- 在制品(WIP)库存可视性与准确率从70%提升至99%。
- 因缺料/待料导致的停线时间减少75%。
- 计划排产准确率提升至90%以上,插单响应速度提升50%。
- 客户满意度与增长:
- 交付准时率(OTD)跃升至98%,主机厂罚款大幅减少。
- 凭借敏捷响应和透明沟通,赢得关键新项目,客户份额(尤其是新能源客户)增长30%。
- 成本与质量双赢:
- 计划、物控、仓库等部门减少数据协调岗位5人,年节省人力成本超60万元。
- 质量数据实时采集与分析,促进过程改善,关键工序不良率下降25%,质量追溯时间从小时级降至分钟级。
- 库存周转率提升20%,呆滞料显著减少。

四、汽配行业的启示录
“ERP是骨架,CRM是神经,车间数据才是驱动智造的血液”——当血液无法在车间、仓库、计划、客户之间畅流,再先进的系统也是“空中楼阁”。
骏驰汽配的蜕变深刻印证:汽配企业的数字化升级,核心不在于颠覆性技术堆砌,而在于打通从客户订单到车间执行的“最后一公里”数据断点。当焊接工人扫描产品码报工的瞬间,当冲压机运行参数实时上传的刹那,数据便跨越了系统间的鸿沟,最终转化为发给主机厂的“准时发货确认函”——这正是汽配供应商在激烈竞争中从生存保供迈向价值共赢的核心密钥。